When you're selecting the fasteners for your project, there's already a world of selections available for your needs. But to complicate things even further, a number of different coatings are available. What are these different coatings and how will they impact your project in the long run? Here's a quick look at several common fastener materials and coatings and in what situations they work best.

Bright
Bright generally refers to steel that has no coating applied to it. Though it's inexpensive, it's also very vulnerable to corrosion.
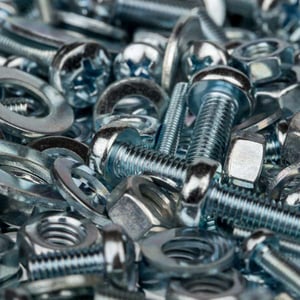
Stainless Steel
Stainless steel fasteners don't have a special coating, but they are significantly more resistant to corrosion, making them a good choice for outdoor and marine applications.
Brass or Bronze
Typically used for decorative purposes in work where the fastener will be left visible, these metals are also very corrosion resistant.
Heat Treated
Heat treating steel fasteners helps harden the metal, making it stronger than it would be otherwise. This makes it an excellent option for masonry or concrete work.
Alloy Steel
Alloy steels often have a dark or black color from an oil or black oxide coating. Though the alloy often strengthens the steel, the coating doesn't provide much corrosion protection.
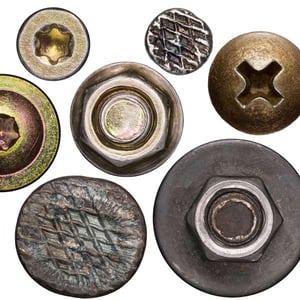
Clear Zinc Plated
This type of coating inhibits rust. It's a relatively inexpensive process that delivers corrosion resistance in humid environments.
Yellow or Electro-Plated Zinc
Much like clear zinc, yellow zinc also provides corrosion resistance. However, it's applied using an electro-plating process, which can create a somewhat different golden color than you would see on clear zinc-plated fasteners.
Hot-Dipped Galvanized
Generally speaking, for better corrosion resistance than standard zinc plating, hot-dipped galvanized coatings provide a thicker layer of zinc on the surface, which makes it a better choice for outdoor use provided that the project location is away from salt water. Though it will corrode, it takes significantly longer than most other coatings.
Chrome- or Nickel-Plated
Though chrome and nickel-plated coatings do provide some level of corrosion resistance to the underlying metal, they are much more commonly used in projects because of their bright, shiny appearance and the aesthetic properties they bring to the project.
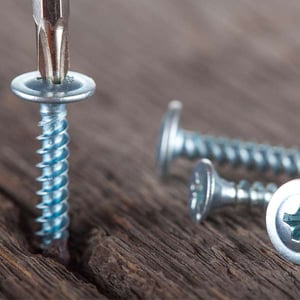
Phosphate Coated
A phosphate coating on a fastener serves to provide lubrication when inserting the fastener by reducing friction. It also improves corrosion resistance, but should only be used indoors. You should also avoid using phosphate-coated fasteners on treated lumber.
Vinyl Coated
Unlike many other coatings, vinyl coated metal doesn't actually gain very much in terms of corrosion resistance. The vinyl acts to reduce friction while driving, while the heat from driving hardens the vinyl, adding some level of holding power.
Ceramic Coated
Ceramic-coated fasteners are often used in marine applications, as the ceramic coating provides protection against salt water spray. They are often designed to pass 500- and 1,000-hour salt spray testing. However, they are not as resistant to corrosion as stainless steel.
By choosing the right material and coating for your project's fasteners, you can ensure that you get the best possible results. But what if you have multiple options available or aren't sure which coating is best for your job? Our experienced associates are ready to help you get the right materials for your project. Please feel free to contact us today for more information or with any questions. At Star Sales, our job is keeping your project moving.